Imagine trying to use a hacksaw to cut through thick steel. Exhausting, right? Now, think about how long that would take and the level of precision you could achieve. In today's fast-paced industrial world, traditional cutting methods just aren't cutting it anymore (pun intended). The problem is, as demand for complex, high-precision metal parts grows, old-school tools can’t keep up. That's where metal laser cutters come in. They're changing the game entirely.
So, why are metal laser cutters the future of fabrication? Simple: they combine speed, precision, versatility, and cost-effectiveness that traditional methods simply can't match. This makes them the go-to solution for industries looking to stay competitive.
But let me break it down a bit further, because it’s more than just speed and accuracy. We’re talking about a technology that’s so versatile, it’s being used everywhere, from automotive manufacturing to cutting out intricate jewelry designs. Stick with me, and I’ll show you why this is the tool of tomorrow.
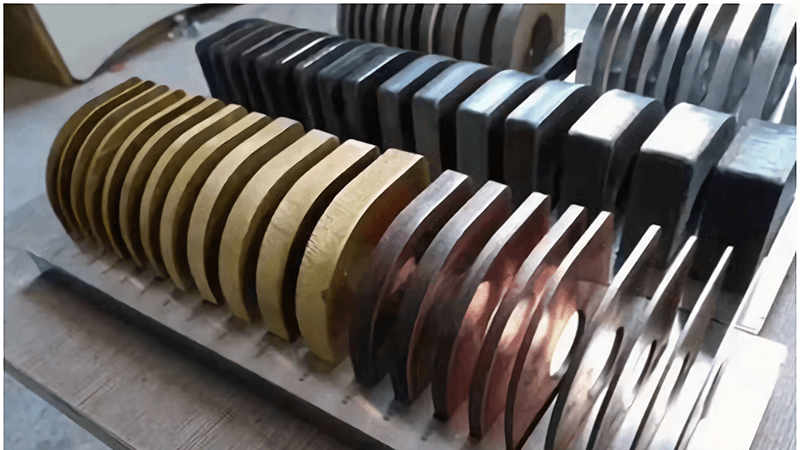
What Makes Laser Cutters So Fast?
Laser cutting isn’t just fast—it’s lightning fast. When you compare the time it takes a laser to slice through metal versus mechanical methods, it’s like comparing a sports car to a bicycle. For instance, cutting a 10mm steel plate? Old school methods might take minutes. A laser cutter? A few seconds.
What’s the secret sauce? Well, lasers focus high-energy light beams onto a small point, melting or vaporizing the material instantly. That means fewer passes, less friction, and a lot less wasted time. Research even shows that using metal laser cutters can reduce fabrication time by up to 50% compared to traditional methods.
Can They Handle Different Materials?
One of the coolest things about laser cutters is that they’re not picky eaters. They’ll chew through stainless steel, aluminum, brass, copper, titanium, you name it. Whether you’re making aerospace parts, crafting medical devices, or even working on consumer electronics, metal laser cutters can get the job done.
And here’s where it gets even better: these machines are so versatile that they can cut complex shapes with little to no secondary processing. Imagine what that does for efficiency! Studies have shown that versatility is one of the top reasons industries are switching to laser technology.
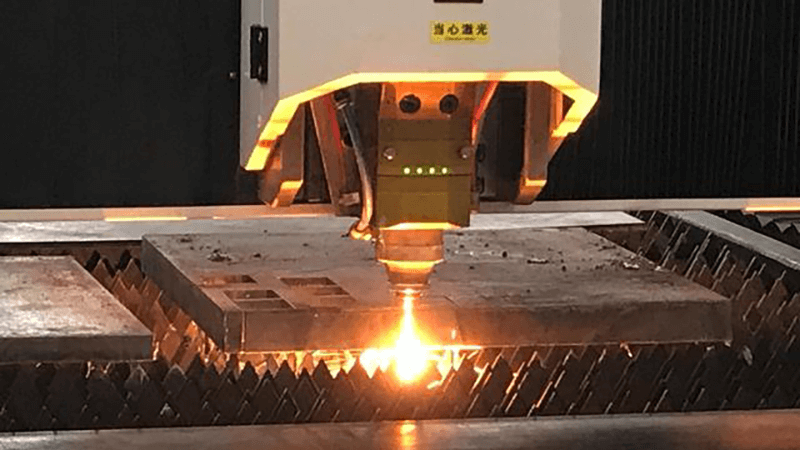
Is Laser Cutting More Efficient and Cost-effective?
Here’s where we get into the juicy part—costs. At first glance, laser cutters might seem like a hefty investment. But when you think about it, they pay for themselves in no time. Why? Two reasons: efficiency and waste reduction.
Traditional methods often require several tools, extra labor, and more time to complete tasks. With laser cutting, you get precise cuts, less material waste, and faster production times. In fact, companies using metal laser cutters report a 30-40% reduction in overall production costs. Plus, the accuracy of the cut means fewer mistakes and do-overs, which further slashes costs.
What About the Environmental Impact?
We can’t ignore the environmental aspect of this discussion. In a world that’s becoming more eco-conscious, metal laser cutters stand out for being environmentally friendly. Traditional cutting processes can be wasteful, leaving behind scraps and excess material. Not with lasers. The precision of the cut means less material is wasted, and the technology itself consumes far less energy.
According to sustainability studies, laser cutting can reduce energy consumption in manufacturing by up to 70% compared to older methods [4]. That’s a win for your budget and the planet.
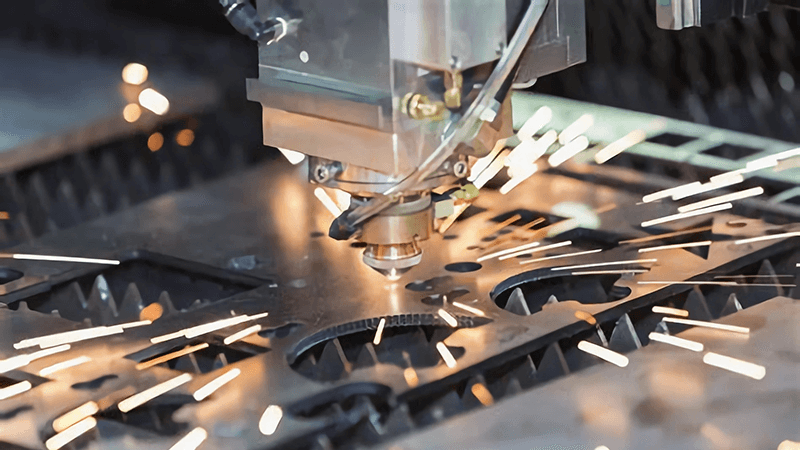
Can Laser Cutters Keep Up with Industry 4.0?
Absolutely. In fact, laser cutters are leading the charge in what’s called "smart manufacturing." These machines can be fully automated, integrated into factory-wide systems, and run 24/7 with minimal human supervision. Imagine a setup where your laser cutting process is fully automated, reducing the risk of human error while significantly boosting productivity.
In this new era of Industry 4.0, where everything is connected, metal laser cutters fit perfectly. They’re smart, adaptable, and easily programmable, making them a staple in modern factories. Automation and smart technology integration are driving the future of laser cutting.
What’s Next for Laser Cutting Technology?
The future of laser cutting is bright—literally. As technologies like fiber lasers continue to evolve, we’re seeing faster, more efficient, and more powerful machines entering the market. Fiber lasers, in particular, are known for their ability to cut reflective metals like aluminum and copper with even greater precision than CO2 lasers.
The real kicker? Future advancements are likely to make these machines more affordable and accessible to smaller businesses. Experts predict a 20% drop in the cost of fiber laser cutters over the next decade [6]. If that’s not futuristic enough for you, I don’t know what is!
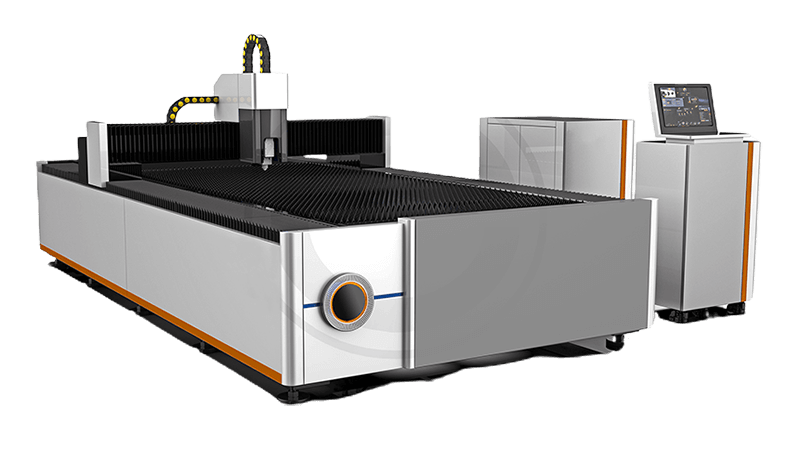
Power: 1.5kw, 2kw & 3kw
Cutting Ability: <14mm
Price: 10,195USD – 15,715USD
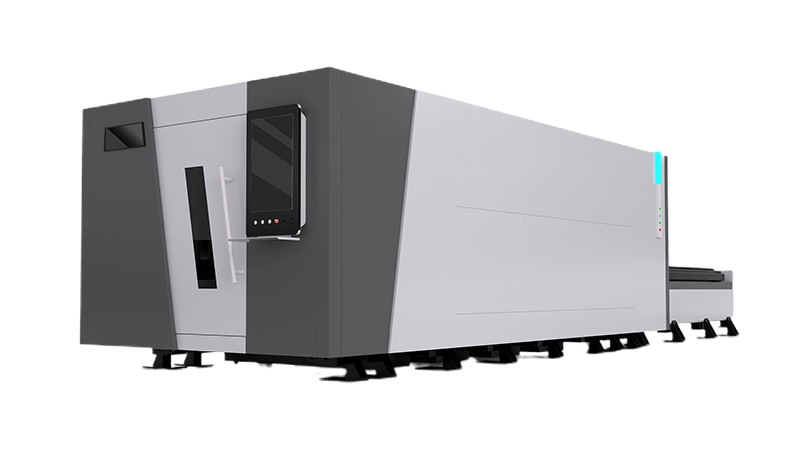
Power: 3kw, 6kw & 12kw
Cutting Ability: <40mm
Price: 25,715USD – 49,850USD
Conclusion: The Future is Laser Cut
Metal laser cutters aren't just the future of fabrication—they're the present. They bring speed, precision, versatility, and sustainability to the table, making them an essential tool in modern manufacturing. If you're in the industry and haven't made the switch yet, you're missing out on a major competitive advantage.
At Kirin Laser, we’ve seen firsthand how our machines have transformed businesses. Let’s talk about how we can do the same for you. Reach out to us, and let’s get started on the future—together.
References:
1>. "5 Benefits of Laser Cutting in Metal Fabrication", from Eckmann Custom Products.
2>. " The Outlook of Metal Cutting and Fabrication in 2024 ", from Davalyn Corporation.
3>. " How to Choose the Best Metal Laser Cutter for Your Needs? “, from Kirin Laser.
4>. " Laser Cutting Steel: Techniques and Best Practices ", from Kirin Laser.