Why Are Laser Welds Taking Over?
When you think of welding, you probably picture sparks flying, heat radiating, and old-school tools. But what if I told you that the future of welding is more precise, efficient, and downright cooler? Laser welding is here to change the game, and it’s not just a trend—it’s a revolution.
Laser welding is gaining popularity because it’s fast, reliable, and perfect for high-precision work. Whether you're in aerospace, automotive, or even jewelry making, this technology offers something for everyone. Here are the key reasons why laser welding is becoming mainstream:
Advantages of Laser Welding:
- High Precision: Laser welding offers extremely high precision, making it ideal for welding small devices and complex structures, ensuring stable weld quality.
- Minimal Heat Affected Zone (HAZ): Compared to traditional methods, laser welding has a much smaller heat affected zone, which means less distortion and material degradation, preserving the original properties of the material.
- Fast Welding Speed: Laser welding is much faster, allowing jobs to be completed in a shorter time, greatly boosting production efficiency.
- Non-Contact Operation: Since the laser beam doesn't physically touch the workpiece, the risk of contamination and damage is reduced, making it perfect for delicate materials and complex parts.
- Wide Material Compatibility: Laser welding can handle a variety of metals like stainless steel, aluminum, and titanium. It can even weld reflective metals, which is often challenging for other welding techniques.
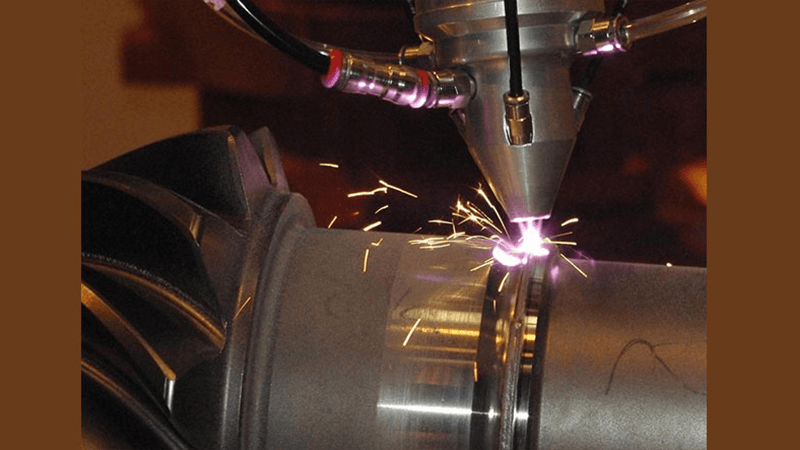
What Is Laser Welding and How Does It Work?
Let me break it down for you. Laser welding is a technique that uses a high-energy laser beam to join materials, often metals. It’s like using a super-focused beam of light to melt and fuse metal parts. Sounds like something from a sci-fi movie, right? Well, it’s happening now in workshops around the world.
The process is simple in theory: the laser beam heats the metal to its melting point, creating a weld pool. The pool solidifies, and boom—you’ve got a solid, high-quality weld. Check out this in-depth look at how lasers weld metal.
The laser welding process involves several key steps:
Preparation of Materials: Before welding, surfaces must be cleaned to remove contaminants such as rust or grease. Proper alignment of the parts is also crucial to ensure a seamless joint.
Focusing the Laser Beam: A high-intensity laser beam is generated using various types of lasers, including solid-state, fiber, and CO2 lasers. The beam is focused on a small area where the materials meet, typically ranging from a few tenths of a millimeter to a few millimeters in diameter.
Melting and Fusion: The concentrated energy from the laser beam heats the material to its melting point, creating a molten pool. As the laser moves along the joint, this molten material cools and solidifies, forming a strong metallurgical bond between the parts.
Cooling and Solidification: After the laser passes, the molten pool solidifies quickly. This rapid cooling helps maintain the integrity of the weld and minimizes heat-affected zones (HAZ), which can lead to material distortion or weakened structures.
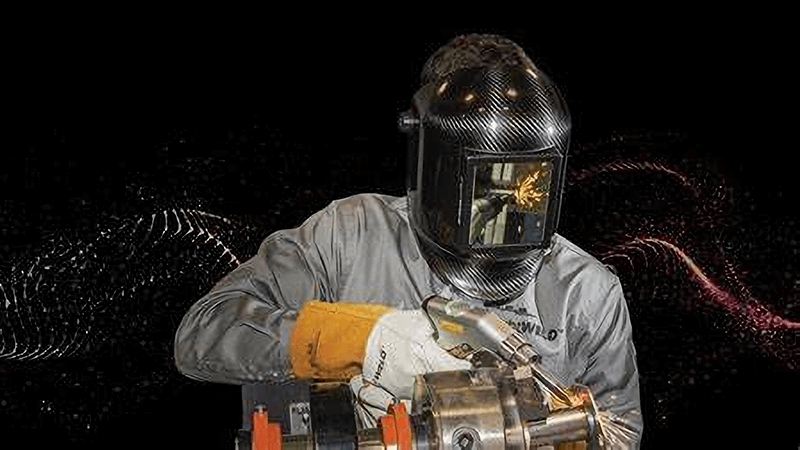
Types of Laser Welding: Which One Is Right for You?
Not all laser welding is the same. There are several types to consider depending on your project needs:
- Description: Uses fiber optics to deliver a concentrated laser beam for welding. It provides high efficiency and excellent beam quality.
- Ideal For: A wide range of materials, particularly in automotive and aerospace industries. Choosing the right type depends on what you’re welding and your end goal.
2. Keyhole Welding
- Description: In this aggressive technique, the laser beam heats the metal to the point of vaporization, creating a "keyhole" effect that allows deeper penetration into thicker materials.
- Ideal For: Heavy-duty applications where speed is crucial, such as automotive manufacturing. However, it may lead to porosity and a larger heat-affected zone (HAZ).
3. Hybrid Laser Welding
- Description: This combines laser welding with traditional arc welding methods (like MIG or TIG) to enhance weld quality and speed. The laser provides precision while the arc adds filler material.
- Ideal For: Complex joint configurations and thicker materials, offering benefits from both welding techniques.
4. Spot Welding
- Description: This technique uses a focused laser to create small, localized welds. It is effective for joining thin materials or making precise connections.
- Ideal For: Electronics and automotive applications where accuracy is paramount.
5. Deep Penetration Welding
- Description: Utilizes high-power lasers to achieve deep welds by vaporizing material at the joint, suitable for thick sections.
- Ideal For: Heavy industrial applications requiring robust joints.
6. Percussion Welding
- Description: Involves pulsing the laser beam at high frequencies to quickly melt and fuse materials, accommodating varying thermal properties.
- Ideal For: Joining dissimilar materials or those with different melting points.
7. Conduction Welding
- Description: This method involves the laser beam slowly melting the metal without reaching vaporization. It relies on heat conduction to fuse materials and is characterized by a smooth, aesthetically pleasing weld.
- Ideal For: Thin metals and applications where high weld strength is not critical. It's often used in industries requiring precision and minimal distortion.
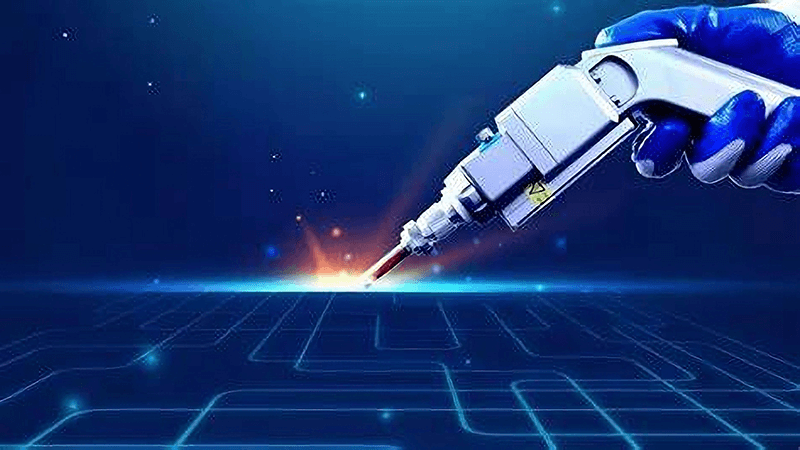
Laser Weld Strength: How Reliable Are Laser Welds?
Now, let’s talk about something important—strength. Laser welds are as strong, if not stronger, than traditional welds. Why? Because they’re precise. The laser creates a cleaner and more uniform weld pool, reducing the chances of weak points.
Strength of Laser Welds:
- High Tensile Strength: Laser welds typically have a strength that's over 90% of the base material’s strength. This is because the focused energy of the laser minimizes defects, resulting in nearly flawless seams.
- Small Heat-Affected Zone (HAZ): One big advantage of laser welding is its ability to keep the HAZ small. This helps reduce thermal distortion and preserves the material’s original properties, leading to stronger joints. In contrast, traditional welding often creates larger HAZs, which can weaken the material.
- Fast Cooling Rates: The quick cooling process in laser welding can cause beneficial microstructural changes, like the formation of martensite in some metals. This can improve the hardness and strength of the weld area.
The strength of laser welds can often outperform traditional methods like TIG or MIG welding, especially when working with high-strength materials. See some data on weld strength comparison below.
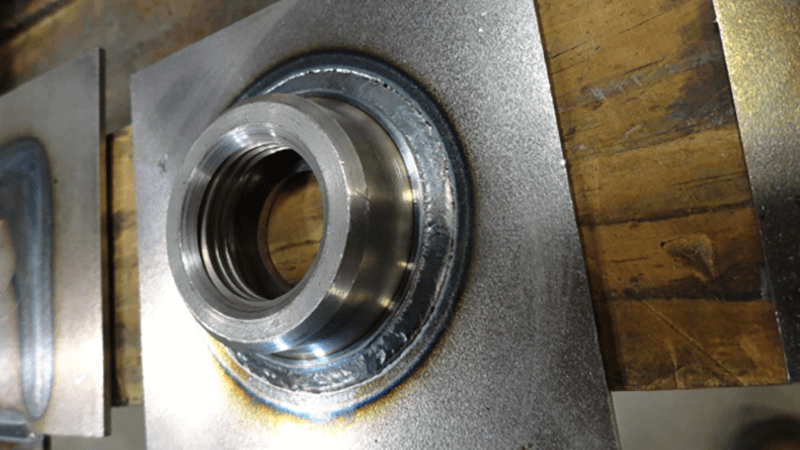
Laser Welding vs. Traditional Welding: What’s the Difference?
Laser welding isn’t just a fancy new toy. It’s a serious competitor to traditional welding techniques. So, how does it stack up?
- Speed: Laser welding is much faster.
- Precision: Less post-processing required.
- Cost: Higher upfront investment, but long-term savings.
Compared to traditional methods like TIG or MIG welding, laser welding reduces the risk of material distortion. That means fewer headaches and more productivity in the long run. Check out a full comparison here.
Comparison of Laser Welding and Traditional Welding
Feature | Laser Welding | TIG Welding | MIG Welding |
Process Type | Fusion process using a focused laser beam | Arc welding using a non-consumable tungsten electrode | Arc welding using a consumable wire |
Welding Speed | 3 to 10 times faster than TIG (up to 100 inches/min) | 2 to 6 inches/min | Moderate speed, varies based on setup |
Heat Input | Low heat input, minimal thermal distortion | High heat input, significant distortion | Moderate heat input, larger HAZ |
Heat-Affected Zone (HAZ) | Small HAZ (0.1 to 1.5 mm) | Large HAZ (2 to 10 mm) | Moderate HAZ |
Weld Quality | High-quality, precise welds with minimal defects | Good quality but larger imperfections possible | Variable quality, prone to spatter and defects |
Material Compatibility | Excellent for thin metals and dissimilar materials | Effective for various metals, especially thick ones | Best for thicker metals, less versatile |
Initial Equipment Cost | Higher initial investment | Moderate initial investment | Lower initial investment |
Ease of Operation | Requires skilled operators but easier to learn | High skill requirement | Easier for beginners |
Post-Weld Processing | Minimal cleanup required | Significant cleanup often needed | Moderate cleanup required |
Applications | Automotive, aerospace, electronics, medical devices | General fabrication, repair works | Heavy manufacturing, construction |
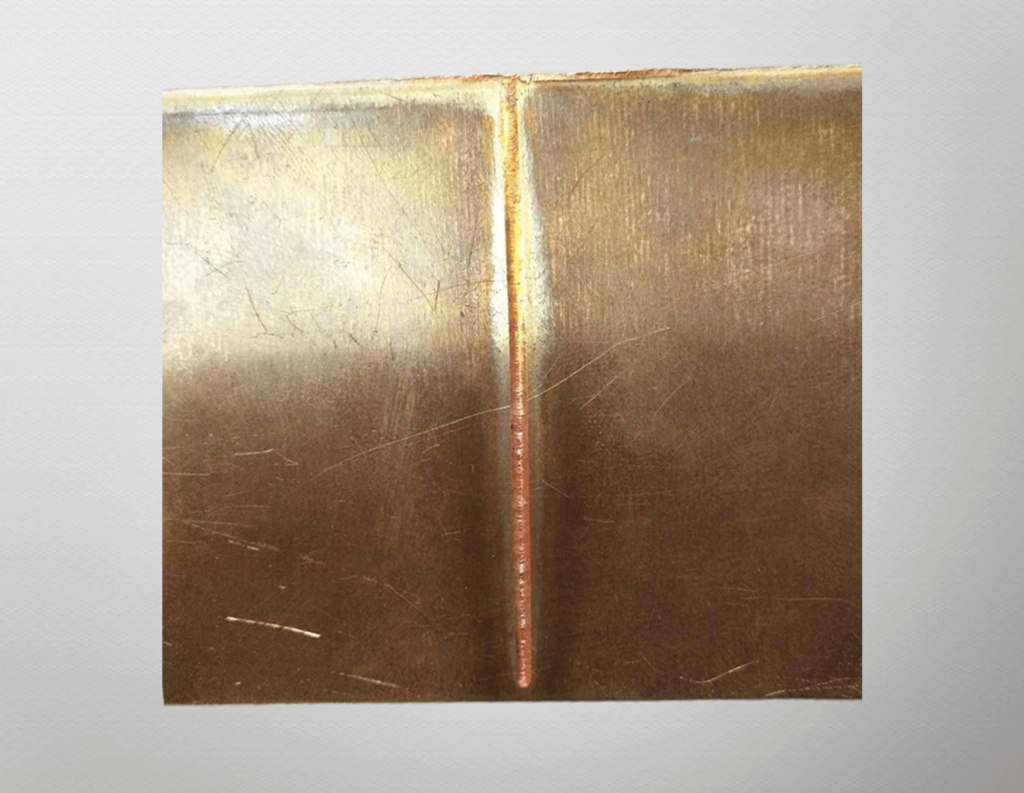
How Does Laser Welding Affect Different Materials?
Not all materials are created equal when it comes to laser welding. Some love the heat, while others… not so much. Here’s a quick guide to how it performs:
Laser Welding Steel
Performance and Uses: Steel works great with laser welding because it absorbs laser energy well, leading to strong welds with minimal distortion. It's commonly used in industries like automotive, where high-quality welds are needed with less heat damage to the material.
Laser Welding Aluminum
Challenges and Fixes: Aluminum can be tricky due to its high reflectivity and thermal conductivity. This makes it harder to control the melt pool, which can cause issues like cracks or pores. To get good results, you need to carefully manage laser settings like power, speed, and focus. Preheating the material and using the right gases can also help improve weld quality and avoid problems like dark welds or incomplete fusion.
Laser Welding Titanium
Advantages and Key Points: Titanium is popular in aerospace because of its great strength-to-weight ratio and resistance to corrosion. Laser welding is ideal for titanium since it allows precise control over the heat, reducing distortion compared to other methods. However, you need to carefully adjust the laser power and speed to avoid defects like porosity. Also, because titanium reacts with air at high temperatures, you must use shielding gases to protect the weld from oxidation and maintain its strength.
Different materials react differently to the laser’s heat, so you’ll want to tailor your settings based on what you’re working with. See how laser welding performs on different metals.
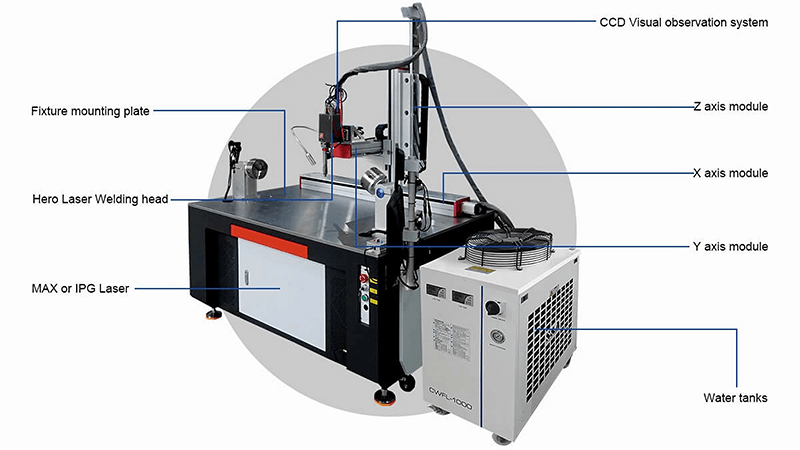
Challenges of Laser Welding: What Do You Need to Watch Out For?
It’s not all sunshine and rainbows. Laser welding has its challenges, and if you're not careful, you could end up with a bad weld. Common issues include:
- Porosity: Tiny bubbles in the weld can weaken it.
- Cracking: Some materials, especially aluminum, are prone to cracking.
But don’t worry—most of these problems are avoidable with proper setup and technique. Here's how to troubleshoot common laser welding issues.
Can You Trust Laser Welding for Complex Projects?
Absolutely! One of the biggest perks of laser welding is its precision. You can work on intricate parts, delicate designs, and even hard-to-reach spots. It’s used in everything from medical devices to complex aerospace components.
The precision of laser welding makes it indispensable for industries requiring exact measurements and flawless finishes. Read more about complex laser welding projects here.
Choosing the Right Laser Welding Equipment
Now that you're convinced laser welding is the future, how do you choose the right machine? You’ll want to consider:
- Power: Higher power for thicker materials.
- Portability: Do you need a stationary or handheld machine?
- Cooling System: Air or water-cooled? Both have their pros and cons.
We at Kirin Laser offer some of the best machines in the market. Our KR-2000 water-cooled welding machine is perfect for high-demand industries, while the KR-1500A air-cooled machine offers mobility and efficiency. Learn more about our models here.

Power: 1.5kw – 3kw Water Cooling
Functions: Welding, Cutting, Cleaning & Seam Cleaning
Price: 1,950 – 4,630USD
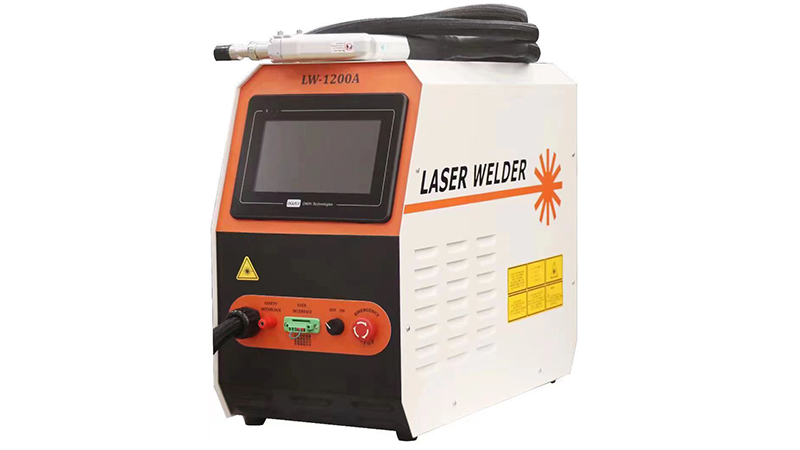
Power: 800w – 2000w Air Cooling
Functions: Welding
Price: 2,250 – 6,630USD
Conclusion: Is Laser Welding the Future of Manufacturing?
In short, yes! Laser welding offers unmatched precision, speed, and reliability. Whether you're in the market for a small setup or a powerful industrial-grade machine, laser welding is the way to go.
If you’re looking to upgrade your operations, we at Kirin Laser have you covered. Contact us today to explore how our machines can transform your business!
1>. " Top Welding Lasers for High-Quality Welds", from Kirin Laser.
2>. "How to Find the Best Laser Welding Machine Prices?", from Kirin Laser.
3>. " Top Benefits of Using Laser Machine Welding", from Kirin Laser.
4>. "Effect of laser power on microstructure and mechanical properties of Nd: YAG laser welding of titanium tubes", from Springer Nature.