Have you ever wondered how those perfectly precise holes are drilled into glass? Imagine being able to achieve such precision in your projects. As the engineer of Kirin Laser, I’ve seen firsthand how laser drilling can transform glass processing. Let me take you through the essential steps and considerations to master this technology.
Laser drilling in glass processing is a game-changer. The precision, speed, and efficiency it offers are unparalleled. In this guide, we'll dive into the nitty-gritty of laser drilling, from preparation to post-processing, ensuring you achieve the best results every time.
Curious to know more? Let’s explore this fascinating world together. Whether you’re a seasoned professional or a curious newcomer, there’s always something new to learn about laser drilling.
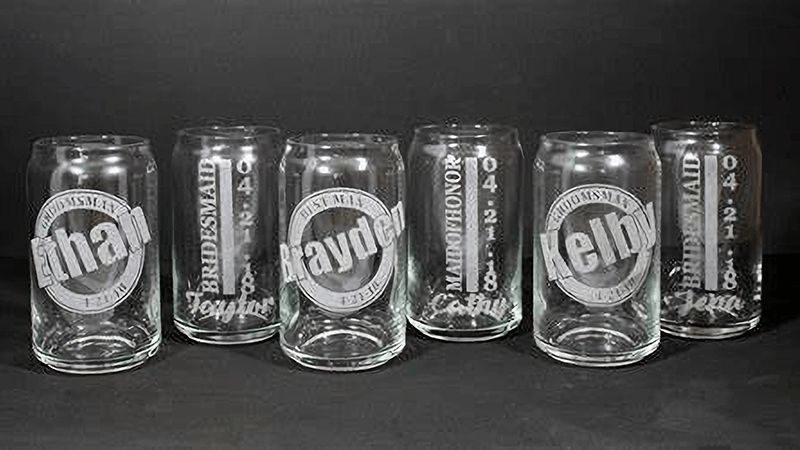
What Are the different types of glass and their processing characteristics?
Glass, with its excellent transparency and chemical stability, is widely used in various fields. In the special glass sectors such as medical, chemical, and photovoltaic, the demand has been increasing annually with the advancement of technology. Below are some common classifications of glass and their processing characteristics:
1>. Soda-Lime Glass, Ultra-Clear Glass, and K9 Glass
- Soda-Lime Glass (Ordinary Glass)
- Ultra-Clear Glass (Low-Iron Glass)
- K9 Glass These types of glass have good toughness and hardness, suitable for drilling holes with thicknesses ranging from 0-20mm.
2>. Borosilicate Glass and Quartz Glass
- Borosilicate Glass: Excellent light transmittance and very low thermal expansion coefficient.
- Quartz Glass: Commonly used in optical lenses, with extremely high hardness. When processing these types of glass, methods such as thermal expansion and contraction or laser cleaving are typically used. With the continuous development of laser technology, laser drilling in glass has gradually become a new processing choice. For processing high-hardness glass, high peak power lasers are required.
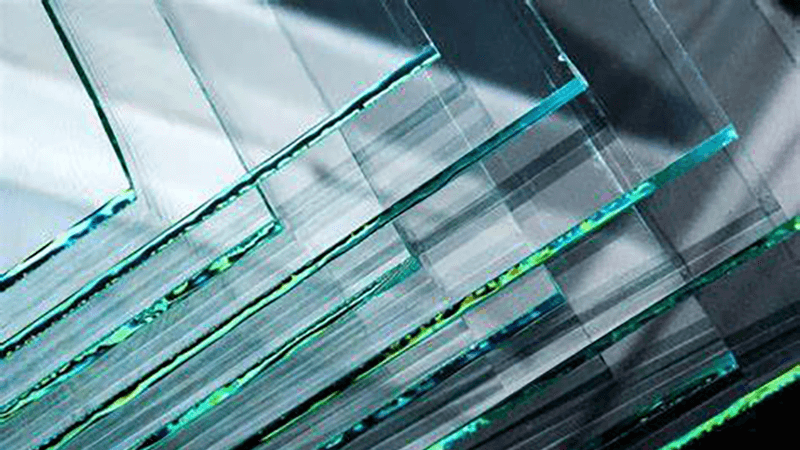
3>. Tempered Glass
Tempered glass is a type of pre-stressed glass that enhances the strength and load-bearing capacity of the glass through chemical or physical methods to form surface compressive stress. Its resistance to wind pressure, cold and heat, and impact have all been enhanced. However, tempered glass cannot be cut after processing. When broken, the fragments of tempered glass form obtuse-angled particles, reducing injury risk to humans.
Different types of glass have their respective advantages and processing requirements in various application scenarios. Choosing the right processing method and tools is crucial to ensuring processing quality.
Advantages of Glass Laser Drilling
Glass drilling is a critical part of glass production and deep processing, highlighting its importance. Currently, traditional glass cutting processes mainly include tool-based CNC cutting and water jet CNC cutting. For small enterprises or those with limited budgets, these traditional cutting methods are difficult to promote due to high costs.
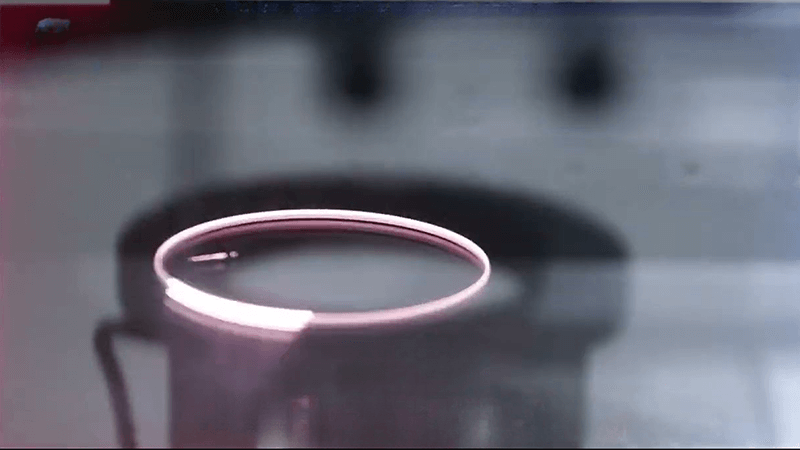
Laser glass drilling, as a non-contact processing method, uses a focused high-energy-density laser beam to melt or even vaporize the glass. The laser utilizes the transparency of the glass to focus the beam on the lowest layer of the glass. By using a 2.5D galvanometer for high-speed scanning, the glass is removed layer by layer from the bottom up, allowing the processing of different thicknesses and types of glass. Besides the initial cost investment, laser cutting glass does not require subsequent consumable costs, making it an increasingly important choice in the glass processing industry.
In this experiment, a Jept YDFLP-M8-200-S-W-V2 laser, combined with a 2.5D galvanometer and a three-dimensional cutting software and hardware system, is used to achieve regular round holes or irregular glass drilling and cutting. Compared to traditional mechanical drilling, this system offers high processing efficiency, low maintenance costs, and minimal thermal impact.
01 Effect of Laser Parameters on Glass Laser Drilling
1>. Impact of Pulse Width on Glass Drilling
Below are the drilling experiments on ultra-clear glass with a hole diameter of 10mm and a thickness of 3mm. The tests were conducted using 6ns, 9ns, and 12ns modes to observe the effect of pulse width on glass cutting at the corresponding cut-off frequencies.
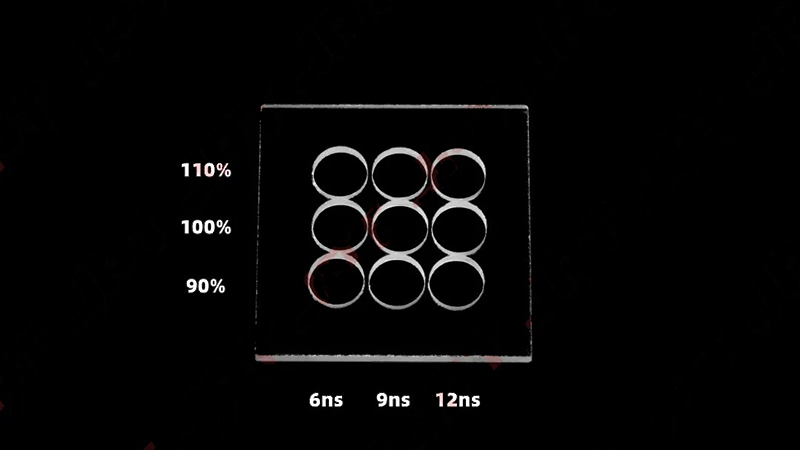
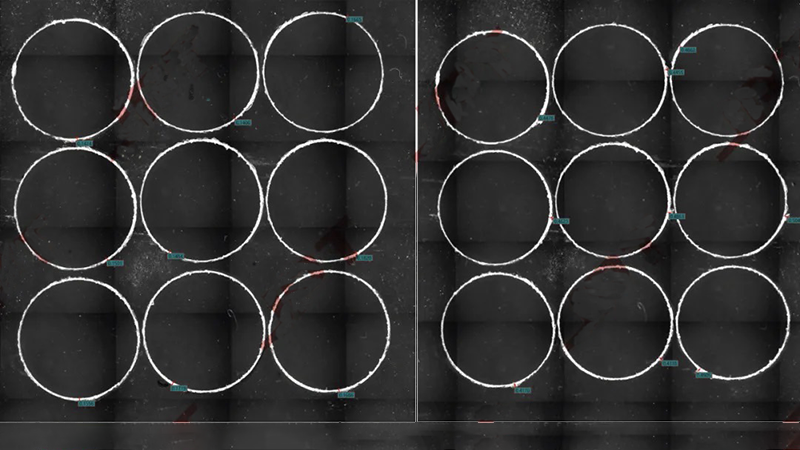
Collapse (μm) \ Pulse Width | 6ns | Difference | 9ns | Difference | 12ns | Difference |
110% Cut-off Frequency P | 147.4 | 431.8 | 140.6 | 314.7 | 166.5 | 366.8 |
Max | 579.2 | 455.3 | 533.3 | |||
Cut-off Frequency P | 150.1 | 249.2 | 148.4 | 299.9 | 182.0 | 302 |
MAX | 399.3 | 448.3 | 484.0 | |||
90% Cut-off Frequency P | 155.6 | 273.8 | 171.9 | 243.6 | 168.6 | 494.1 |
MAX | 429.4 | 415.5 | 662.7 |
The experiment concludes that the average and maximum values of edge collapse for 9ns are the best controlled, followed by 6ns, which also exhibits good edge collapse performance. The average and maximum values for 12ns are slightly larger, with the analysis indicating that heat accumulation at 12ns causes the edge collapse. Suitable single pulse energy and peak power significantly impact edge collapse control. Higher single pulse energy and higher peak power under the same pulse width result in better processing effects.
2>. Effect of Repetition Frequency on Glass Drilling
The experiment concludes that when the repetition frequency is at the cut-off frequency, the processing efficiency is the highest. The reduced processing time decreases heat accumulation, resulting in the smallest edge collapse compared to 90% and 110%. Below the cut-off frequency, the lower average output power leads to lower efficiency. Above the cut-off frequency, the decrease in single pulse energy and peak power results in lower efficiency.
Processing Time \ Pulse Width | 6ns | 9ns | 12ns |
110% Cut-off Frequency | 1.977s | 1.816s | 1.529s |
Cut-off Frequency | 1.907s | 1.791s | 1.434s |
90% Cut-off Frequency | 2.167s | 1.866s | 1.618s |
3>. Effect of Power on Glass Drilling
The power of the laser affects both the efficiency and the processing time. To further explore the significant impact of laser power on efficiency, the experiment was conducted by changing only the power percentage while keeping other parameters constant. The parameters chosen were the 9ns mode with a frequency of 280k, and the power percentages were set at 70%, 80%, and 90%. The efficiency of drilling a 10mm diameter hole in 3mm thick white glass was tested.
The experiment concludes that as the average power increases, the peak power of the laser increases, and the time required to drill holes of the same thickness and diameter decreases.
Power Percentage | Time |
70% | 2.622s |
80% | 1.919s |
90% | 1.447s |
02. Laser Irregular Drilling Experiment
The laser beam is output by the laser, and the galvanometer motor achieves high-speed movement of the laser beam through high-speed motion, which is then focused into the working range by the F-Theta lens. This processing method is convenient, controllable, and adjustable, providing a competitive solution for the automation and integrated processing of equipment.
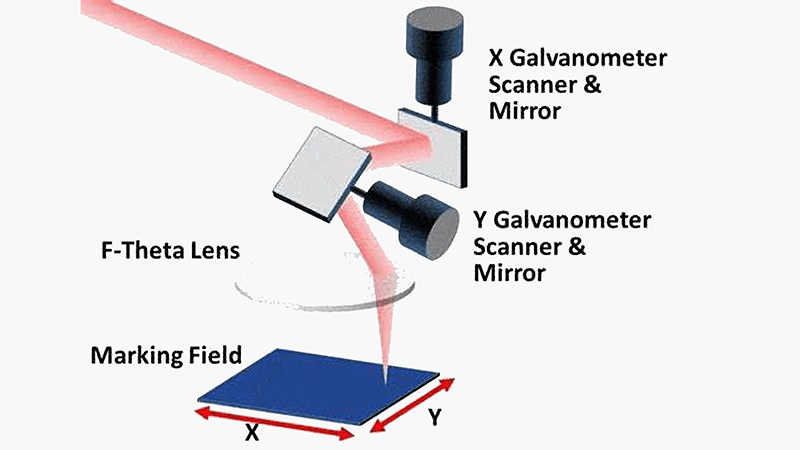
The image below shows the irregular drilling effect using the YDFLP-200-M8-S-W-V2 laser, with edge collapse less than 400 micrometers and excellent edge quality.
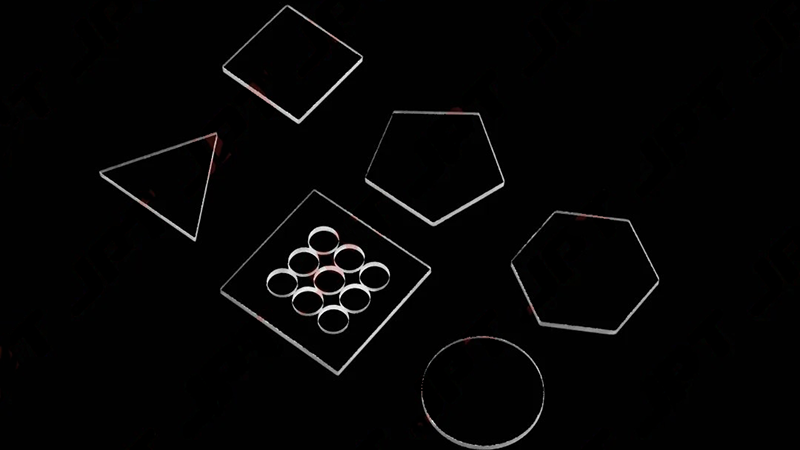
03. Different Thickness Glass Laser Drilling Experiment
In the glass drilling industry, improving efficiency and reducing costs are common pursuits. Addressing industry pain points and challenges is the relentless goal of JPT. Greater single pulse energy and higher peak power significantly improve processing efficiency. The following results show the processing efficiency for different thicknesses and drilling diameters using the YDFLP-200-M8-S-W-V2 laser, for reference only.
Drilling diameter (mm) | Drilling time(s) | ||
0.3 | 0.8 | 1.1 | 3.4 |
10 | 1.0 | 1.6 | 3.3 |
20 | 1.8 | 2.4 | 6.7 |
30 | 2.8 | 4.8 | 11.5 |
40 | 4.7 | 6.8 | 15.9 |
50 | 5.5 | 8.6 | 20.0 |
60 | 9.1 | 13.3 | 23.0 |
70 | 14 | 16.0 | 29.0 |
80 | 17 | 27.0 | 40.0 |
100 | 24 | 43.0 | 81.0 |
120 | 47 | 80.0 | / |
150 | 63 | / | / |
04. JPT M8 Series Lasers
The JPT M8 series lasers adopt a Master Oscillator Power Amplifier (MOPA) structure. Since its launch in 2021, it has undergone multiple iterations and optimizations, developing various power levels of lasers for different applications. Low to medium power lasers (such as 20W and 50W) are suitable for surface treatment and etching of heat-sensitive materials. Medium to high power lasers (100W to 300W) perform excellently in high-efficiency, high-demand applications such as deep cutting, deep engraving, and glass frosting.
Building on the independently adjustable pulse frequency feature of the JPT M7 series, the M8 series focuses on optimizing pulse peak power and beam quality. This series maintains excellent beam quality under high-power operating conditions, with peak power reaching up to 300KW. The efficient M8 series lasers bring a new level of high-efficiency processing to the industrial automation field.
Parameter | Specification | Remarks |
M² | < 1.5 | / |
Average Output Power (W) | > 200 | / |
Pulse Energy (mJ) | 0.95 mJ @ 12ns | / |
Pulse Width (ns) | 6-200 | Adjustable |
Maximum Peak Power (kW) | 300 | / |
Repetition Frequency (kHz) | 1-4000 | Adjustable |
Output Power Instability (%) | < 5 | 24h |
Central Wavelength (nm) | 1064 | / |
Beam Diameter (mm) | 3 ± 0.5 or 11 ± 1 | / |
Power Adjustment Range (%) | 0-100 | / |
Spectral Width @ 3dB (nm) | < 20 | 3dB Bandwidth |
Polarization Direction | Arbitrary | / |
Anti-Reflection Capability | Yes | / |
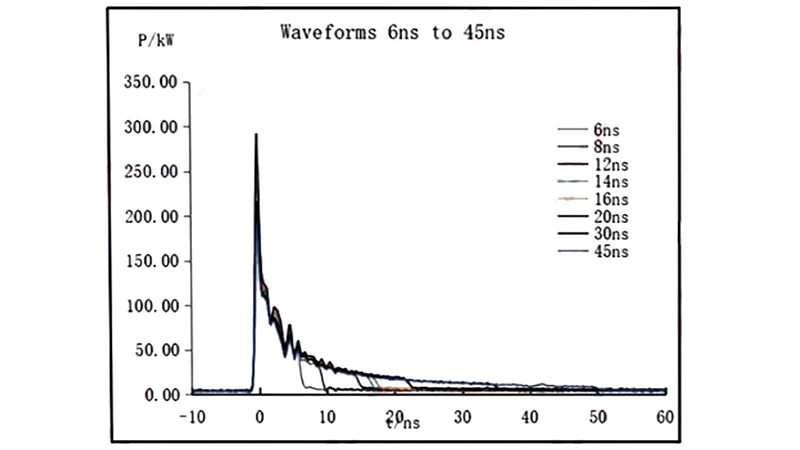
05. Applications for Complex Material Characteristics
The high peak power lasers of the M8 series can achieve effects that ordinary infrared fiber lasers cannot, such as marking on plastics. There are many common types of plastics, and usually, 1064nm infrared fiber lasers are considered unsuitable for marking on plastic materials, with UV solid-state lasers or CO2 lasers being commonly used. However, the low heat characteristics of high peak power lasers make this marking possible.
Compared to the various problems present in traditional contact processing, the non-contact processing method of high peak power, high-power lasers has significant advantages. Although the initial investment is larger, the subsequent processing stability is stronger, and continuous investment is less. In applications with complex material characteristics and physical properties, the JPT M8 series high peak power lasers, with their excellent beam quality and adjustable parameter options, can easily handle and complete high-quality processing.
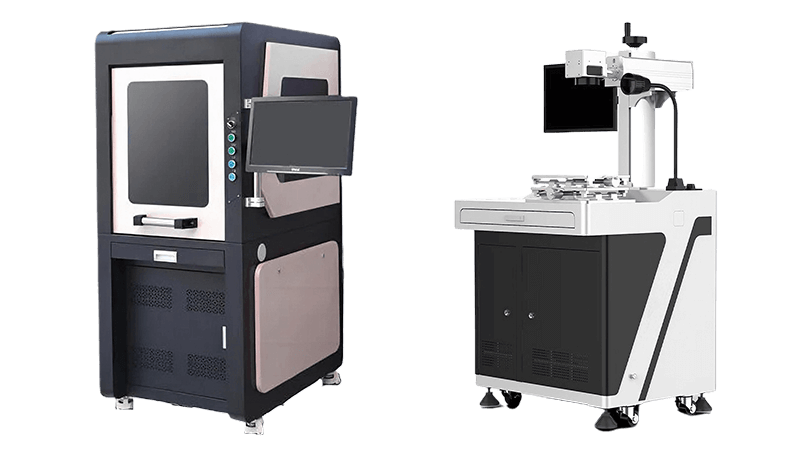
Conclusion
Laser drilling in glass processing offers unmatched precision and efficiency. Different types of glass have their respective advantages and processing requirements, and understanding these is crucial for achieving optimal results. Laser technology, especially with advancements like the JPT M8 series lasers, provides a versatile and efficient solution for various glass processing needs. By selecting the right type of glass, setting appropriate parameters, and utilizing advanced laser systems, you can significantly enhance your glass processing capabilities. Embrace the future of glass processing with laser technology and take your projects to new heights! Contact us to get more details.