Are you tired of struggling with subpar laser cutting results? You’re not alone. Many face issues like poor edge quality or wasted material, leaving them frustrated and out of pocket. The good news? You can turn it around by optimizing your process. Let’s dive in and transform how you approach laser cutting.
The secret to better laser cutting results lies in fine-tuning your setup, from choosing the right parameters to maintaining your machine. A few tweaks can mean the difference between frustration and flawless cuts.
Want to see how small adjustments can make a big impact? Keep reading; I’ll show you the ropes with a touch of wit and practical advice.
Why Do Laser Cutting Results Matter?
Ever wonder why some manufacturers get perfect cuts while others struggle? Precision isn’t just about aesthetics. It affects assembly, production speed, and ultimately, your costs. Inconsistent results can lead to waste or rejected parts, costing you time and money.
And here’s the kicker: poor results often boil down to avoidable mistakes. You don’t need to be a rocket scientist to fix them—just a little guidance, like the kind we offer at Kirin Laser.
Key Factors for Achieving High-Quality Laser Cutting Results
Achieving a high-quality laser cutting outcome requires a combination of precision, accuracy, and operational efficiency. Here are the critical attributes that define a successful laser cutting process:
- Precision and Accuracy
Tight Tolerances: A well-executed laser cut should achieve tolerances within ±0.1 mm or better. This is essential for projects that demand intricate designs and exact dimensions.
Minimal Deviation: Consistency in cuts, typically within ±0.05 mm, reflects a properly calibrated laser cutter. This ensures that each part is nearly identical, meeting stringent quality standards. - Cut Quality
Smooth Edges: A clean, smooth edge with minimal burrs or roughness is ideal. Surface roughness should be kept under 10 micrometers to avoid additional finishing processes that could affect production efficiency.
Clean Cuts: A high-quality cut should have no slag or dross. Clean edges reduce the need for post-processing, making the operation more efficient. - Heat-Affected Zone (HAZ)
Minimized HAZ: The heat-affected zone should be as small as possible to prevent thermal distortion or material property changes around the cut. This results in better mechanical properties for the finished part. - Verticality and Alignment
Straight Cuts: For thicker materials, maintaining verticality is essential. Ensuring straight cuts helps parts fit together accurately and keeps their structural integrity intact.
Proper Alignment: Ensuring the laser beam is properly aligned minimizes deviations, which is crucial for consistent quality in multiple cuts. - Material Utilization
Efficient Nesting: Efficient nesting maximizes the use of the material and reduces waste. This not only optimizes resources but also helps in minimizing overall production costs. - Operational Stability
Consistent Power Supply: A steady power supply ensures consistent laser performance, maintaining uniform cutting speed and quality throughout the process. - Overall Efficiency
Reduced Production Time: High-speed cutting and minimal downtime between jobs result in faster production times. The goal is to meet quality standards while optimizing overall operational efficiency.
Laser cutting requires precise parameter adjustments for optimal results.True
Properly adjusting power, speed, and focus to match material properties is essential for achieving high-quality cuts.
Regular machine maintenance improves cutting precision and extends the lifespan of the equipment.True
Routine maintenance tasks, like cleaning lenses and lubricating moving parts, help maintain the machine's performance and reduce breakdowns.
Key Factors That Impact Laser Cutting
Several variables affect your laser cutting results. The first is material quality. Cheap or inconsistent materials can cause irregularities in cuts, no matter how perfect your machine setup is. Invest in reliable suppliers—it pays off in the long run.
Next up: machine maintenance. Neglecting maintenance is like expecting a car to run without oil. Clean lenses, aligned beams, and proper calibration keep your machine humming.
Learn more about machine maintenance here.
Proper maintenance of a laser cutting machine is essential for ensuring peak performance, extending its lifespan, and ensuring safety. Regular upkeep reduces the likelihood of malfunctions and expensive repairs while boosting productivity. Here’s a guide to effective maintenance practices and schedules.
1. Daily Maintenance Tasks
- Clean the Work Area: Make sure to clear any metal debris and dust from the cutting table daily to avoid contamination in the cutting process.
- Inspect the Cutting Head: Check that the laser cutting head is clean and free from obstructions. Clean the focusing lens and mirrors as necessary to preserve cutting precision.
- Lubricate Moving Parts: Apply lubricant to the guide rails and other moving components to ensure smooth operation and minimize mechanical wear.
- Check Gas Pressures: Confirm that the pressures of auxiliary gases are within the recommended range before starting the machine.
- Remove Slag and Debris: After each operation, clear away any slag or waste materials to keep the work area neat and prevent interference with future tasks.
2. Weekly Maintenance Tasks - Deep Clean Components: Use appropriate cleaning solutions (like acetone or alcohol) to clean the lens and check mirrors for dust buildup. Use a soft cloth to avoid damaging sensitive surfaces.
- Inspect Drive Systems: Examine the motors, gearboxes, and couplings for any debris or signs of wear. Ensure they operate smoothly without unusual sounds.
- Check Cooling System: Make sure coolant levels are adequate and inspect for any leaks. Replace coolant if necessary to maintain cooling efficiency.
- Clean Dust Collection System: Regularly clean dust collection baskets, particularly during high-use periods, to ensure effective dust removal.
3. Monthly Maintenance Tasks - Replace Worn Parts: Examine parts such as belts, gears, and bearings for wear and replace them as needed to prevent unexpected failures.
- Update Software: Check for the latest software updates to ensure the machine benefits from new features and optimized settings.
- Check Electrical Systems: Inspect power supplies, cables, and connections for corrosion or wear. Ensure everything is securely connected to prevent electrical issues.
4. Annual Maintenance Tasks - Professional Service Check: Schedule an annual inspection by a certified technician to evaluate all major systems, replace worn-out parts, and recalibrate the machine for top performance.
- Complete System Review: Perform a thorough review of the machine’s operational performance, maintenance logs, and any recurring error codes to identify potential issues that need attention.
This is a maintenance schedule for your laser cutting machine, designed to ensure optimal performance, extend its lifespan, and prevent unexpected breakdowns. By following the tasks outlined in the table, you can efficiently manage your machine’s upkeep, maximize productivity, and minimize repair costs. Use this schedule as a reference to keep your laser cutting machine operating at its best.
Maintenance Task | Daily | Weekly | Monthly | Annually |
---|---|---|---|---|
Clean Work Area | ✔️ | |||
Inspect Cutting Head | ✔️ | |||
Lubricate Moving Parts | ✔️ | |||
Check Gas Pressures | ✔️ | |||
Remove Slag & Debris | ✔️ | |||
Deep Clean Components | ✔️ | |||
Inspect Drive Systems | ✔️ | |||
Check Cooling System | ✔️ | |||
Clean Dust Collection | ✔️ | |||
Replace Worn Parts | ✔️ | |||
Update Software | ✔️ | |||
Check Electrical Systems | ✔️ | |||
Professional Service Check | ✔️ | |||
Complete System Review | ✔️ |
What Problems Can Arise in Laser Cutting?
Let’s talk dross—the bane of every laser operator’s existence. This molten material sticks to edges and makes your parts look sloppy. Often, it’s caused by improper assist gas or incorrect focus settings.
Then there’s burn marks. They can turn a masterpiece into a mess. Using protective films or optimizing cutting speed can help eliminate these pesky blemishes.
Explore solutions to laser cutting issues.
Problem | Causes | Solutions |
---|---|---|
Inconsistent Cutting Quality | Variations in material thickness Incorrect laser settings or machine calibration |
Regularly calibrate the laser power, cutting speed, and focus position for each material. Conduct test cuts on scrap material before production. |
Incomplete Cuts | Insufficient laser power for the material thickness Misalignment of the laser beam |
Increase the laser power settings for adequate penetration. Check and adjust focus position to align with the material surface. |
Dross Formation | Incorrect settings for power, speed, and assist gas pressure Worn-out nozzle |
Adjust laser power and cutting speed settings to minimize dross. Increase assist gas pressure and inspect/replacing worn-out nozzles. |
Burr Formation | Insufficient assist gas flow Low laser power setting |
Increase assist gas pressure and adjust laser power settings to reduce burrs. |
Rough Edges or Striations | Excessive cutting speed Low assist gas pressure |
Decrease the cutting speed and increase assist gas pressure for smoother edges. |
Kerf Width Issues | Out-of-focus laser beam Incorrect material positioning |
Check and adjust focus spot size. Ensure materials are flat and level on the cutting table. |
Heat-Affected Zone (HAZ) | Excessive heat during cutting altering material properties | Optimize cutting parameters like laser power density and cutting speed. Consider post-cut treatments like annealing. |
Misalignment of Laser Beam | Mechanical wear Improper setup |
Regularly check and adjust the alignment of the laser beam to ensure accurate cuts. |
Tips to Optimize Your Laser Cutting Process
Want insider tips? Let’s start with laser parameters. Adjust your power, speed, and focus to match the material’s properties. Sounds simple, right? But it’s the kind of tweak that can save you hours of rework.
Next, assist gases are your best friend. Whether you’re using nitrogen, oxygen, or air, they play a critical role in achieving smooth edges. Always test your gas flow and pressure before starting.
Finally, efficient nesting strategies can minimize waste. Nesting software helps you maximize material usage while maintaining quality.
Check out nesting tools for laser cutting.
CypCut software, developed by Bochu, is a powerful control system specifically designed for flat laser cutting operations. It offers a wide range of features aimed at enhancing cutting efficiency and precision. Here’s an overview of the main functionalities of CypCut software:
Key Features of CypCut Software
1. Graphic Processing
File Format Support: CypCut supports various graphic file formats, including AI, DXF, PLT, and Gerber, allowing for versatile design imports.
Automatic Optimization: The software automatically optimizes imported graphics by removing duplicate lines, merging connected lines, and eliminating small shapes to streamline the cutting process.
2. Parameter Settings
Customizable Cutting Parameters: Users can configure laser power, frequency, gas type, and pressure based on different materials and cutting requirements.
Flexible Configuration Options: The software provides a range of parameter settings to adapt to various processing needs, ensuring optimal cutting performance.
3. Custom Cutting Process Editing
Path Customization: Users can customize cutting paths and processes, including lead-in settings, kerf compensation, and micro-joint adjustments.
Advanced Features: Supports curve splitting, merging shapes, and converting text to curves for enhanced design flexibility.
4. Nesting Functionality
Automatic Nesting: CypCut includes automatic nesting capabilities that maximize material utilization and minimize waste.
Common Edge Cutting: The software supports common edge cutting and generates leftover materials efficiently.
5. Path Planning
Automatic Path Generation: Automatically generates cutting paths while allowing for manual adjustments to ensure the best cutting results.
Lead-in Checks: Provides automatic recognition of lead-in directions and kerf compensation to enhance cutting accuracy.
6. Simulation and Processing Control
Real-time Simulation: Offers real-time simulation of the cutting process, enabling users to preview the cutting outcome before actual execution.
Processing Control Features: Includes monitoring capabilities during the cutting process, allowing users to make adjustments as needed.
7. Additional Auxiliary Functions
Breakpoint Memory: Supports breakpoint memory functionality, enabling users to resume cutting from any point in case of interruptions.
Material Library Management: Provides robust material library management features for saving and retrieving processing parameters for different materials easily.
8. User-Friendly Interface
Intuitive Design: CypCut boasts an intuitive user interface that simplifies the operation process for both novice and experienced users.
Multi-language Support: The software is available in multiple languages, making it accessible to a global user base.
By integrating these features, CypCut software significantly enhances the operational efficiency of laser cutting machines while ensuring high-quality processing results. Users can flexibly adjust settings according to their specific needs, leading to effective laser cutting operations that meet diverse manufacturing demands.
Cheap materials always result in consistent laser cutting results.False
Inconsistent or low-quality materials can cause irregularities in cuts, no matter how well the machine is set up.
CypCut software supports automatic nesting to minimize material waste.True
CypCut includes automatic nesting functionality, which helps maximize material utilization and reduce waste during the cutting process.
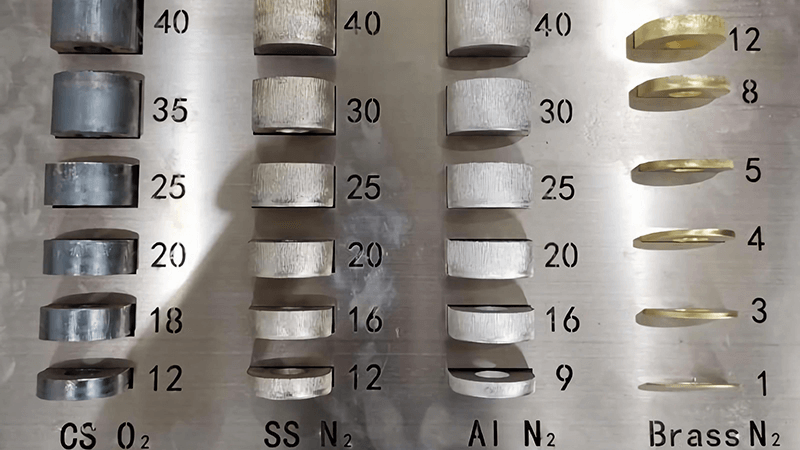
Tools to Help You Achieve Better Results
I always tell my clients: the right tools make all the difference. Process simulation software allows you to visualize and optimize your cutting path before touching the material.
And of course, investing in reliable equipment matters. Kirin Laser’s machines are designed for precision and cost-performance. Our KR-Series Fiber Lasers are a client favorite for their reliability.
Real-World Example
Here’s a story that always makes me proud. One of our clients in the automotive industry struggled with inconsistent cuts on stainless steel. After switching to our KR-Series machine and tweaking their gas flow settings, they saw a 30% improvement in productivity. Their feedback? “Kirin Laser machines turned our frustration into smooth operations!”
Discover more client success stories.
Conclusion
Better laser cutting isn’t a mystery—it’s a combination of knowledge, the right tools, and proactive maintenance. Got questions? At Kirin Laser, we’re here to help you achieve the results you deserve. Reach out to us today, and let’s cut through the challenges together!
Refereces:
- "Why Metal Laser Cutters are the Future of Fabrication?", from Kirin Laser.
- "How to Choose the Best Metal Laser Cutter for Your Needs?" from Kirin Laser.
- "Laser Cutting Steel: Techniques and Best Practices" from Kirin Laser.
- "4 Maintenance tips for Laser Cutting Machines" from Motofil