Imagine this: you're in the market for a new fiber laser welding machine, but you're stuck between two choices—air-cooling and water-cooling. It's like choosing between a sports car and a luxury sedan. Both have their perks, but which one is the perfect fit for your needs? Let's break it down.
Whether it's air cooling or water cooling, both have become the new favorites in the welding industry. Historically, water cooling emerged earlier alongside the popularization of continuous fiber lasers, but air cooling is undoubtedly the rising star. The choice between the two ultimately depends on your specific requirements and circumstances.
As an experienced engineer who has worked extensively with both systems and their diverse applications, I will analyze the differences between them from multiple perspectives, including various customer groups, application scenarios, and technical aspects. This will help you make an informed decision.
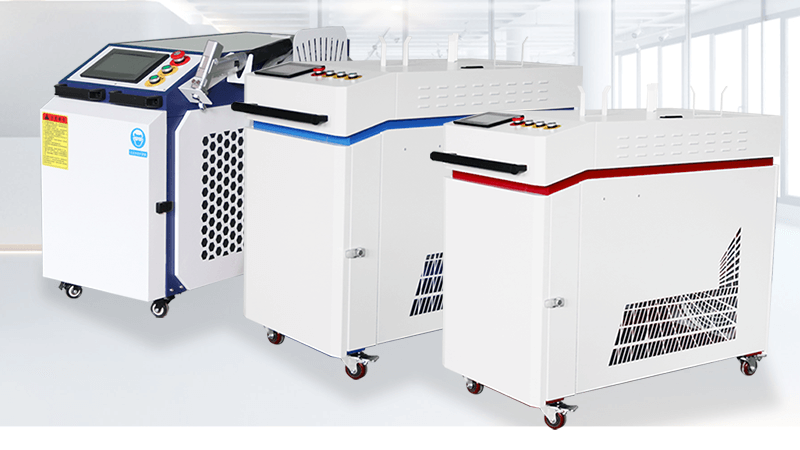
What are the fundamental differences between air-cooled laser welding and water-cooled laser welding?
With the increasing application of fiber lasers, their reliability has become a growing concern. This includes the reliability of laser output performance, electronic components, optical devices, and the overall system. Most of these are closely related to the thermal characteristics of the laser itself. Moreover, temperature significantly impacts the performance of the laser, particularly its output power and stability.
The primary sources of heat in a fiber laser are the pump source and the gain cavity. For the pump source, its conversion efficiency is around 50%, which means that an amount of energy equivalent to the output optical power is generated as heat. If heat is not dissipated promptly, the internal chip temperature will rise rapidly, causing the laser's central wavelength to drift with the temperature increase. In the gain cavity, only part of the pump light is converted into laser output after entering the active gain fiber, with the remaining energy converting to heat. This heat increases the temperature of the gain medium, leading to broadening of the fluorescence spectrum and shortening of the spontaneous emission lifetime, thereby reducing energy conversion efficiency. Therefore, thermal management is of significant importance to fiber lasers.
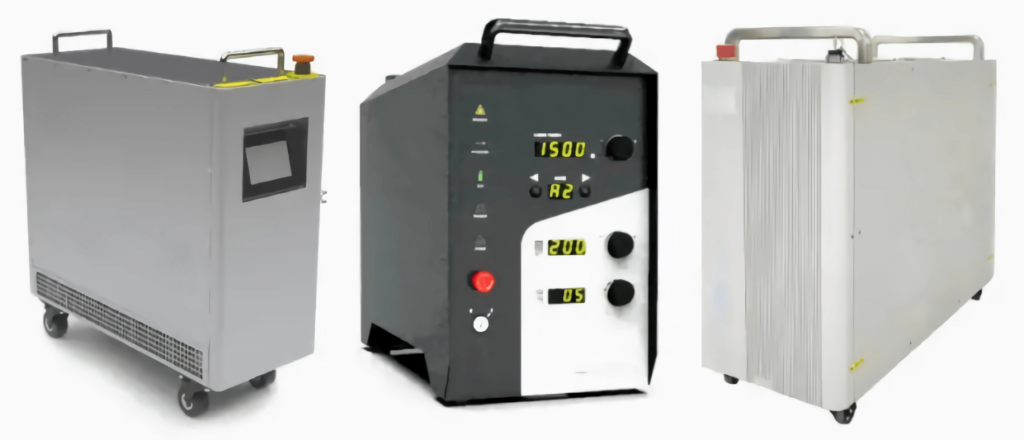
Currently, the common thermal management techniques include air cooling and water cooling. Air cooling is mainly used for low-power pulsed lasers and low-power continuous lasers, while medium to high-power fiber lasers primarily use water cooling as the main cooling measure.
Two Main Cooling Methods
1. Water Cooling
Water cooling, as the name suggests, uses water to remove heat through a heat exchanger (e.g., a water-cooled plate). Its working principle is simple: cold water from the chiller flows into the heat exchanger through pipes and then exits from another port, returning to the chiller through pipes, thus continuously circulating and carrying heat away from the laser. Water cooling systems are simple in structure and easy to maintain, with strong heat dissipation capability and good temperature uniformity. The cooling performance of the laser can be improved by using chillers with higher cooling capacity. Currently, there are about 500 companies on the market that integrate and sell handheld laser welding machines, most of which use water cooling. However, water-cooled handheld laser welding machines require additional chillers and water, significantly increasing the overall size and weight of the equipment and limiting its usage environment.
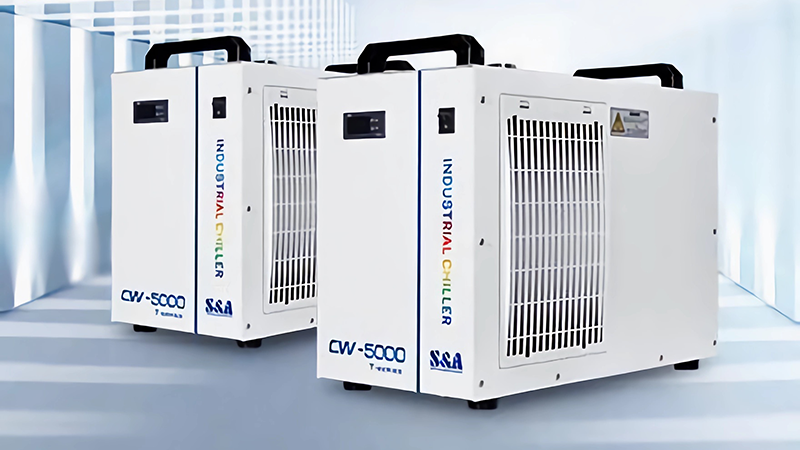
2. Air Cooling
Broadly, air cooling refers to the use of fans to enhance air convection for heat exchange inside the machine. With technological advancements, major laser manufacturers have started exploring air cooling. Last June, global fiber laser giant I company IPG launched the air-cooled LightWELD 1500W handheld laser welding product. In August, GW became the first in China to launch the air-cooled A1500W intelligent laser welding machine. In October, Reci company also released the FCA1500 air-cooled laser. These three lasers target the handheld laser welding market segment. Air-cooled lasers provide more flexibility and portability in operation. They all use air cooling, eliminating the need for additional water-cooling equipment, thereby reducing costs and significantly decreasing the size and weight of the equipment.
Although all are called air-cooled lasers, they adopt different air-cooled solutions: fan cooling, heat pipe cooling, and compressor cooling.
1>. Fan Cooling
In lasers, fan cooling uses a highly thermally conductive substrate (such as copper or aluminum nitride) to transfer heat generated in the pump source and gain cavity to the heat sink. The heat is then dissipated through convection. Convection heat transfer can be classified as natural convection or forced convection depending on the fluid flow driving force. Without external force, fluid spontaneously flows due to temperature differences, which is called natural convection. When driven by external forces such as fans, the fluid flows rapidly, carrying away heat, which is called forced convection.
Natural convection cooling is extremely slow and inefficient, insufficient to meet laser cooling needs. Therefore, fans are added to the cooling system to speed up air flow, turning natural convection into forced convection.
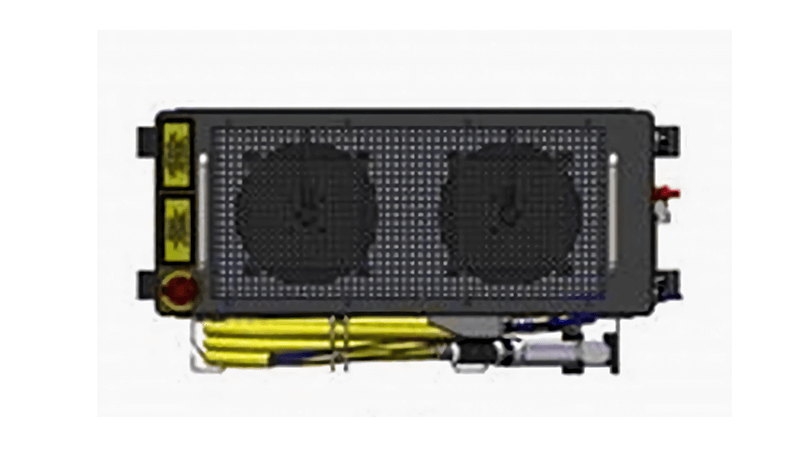
2>. Heat Pipe Cooling
Heat pipe cooling relies on the phase change of the working liquid inside the heat pipe for heat transfer. This liquid has a low boiling point and evaporates easily. One end of the heat pipe (evaporation end) connects to the laser's heat sink, while the other end (condensation end) connects to the external heat sink and fan. The pipe wall contains a wick made of porous material. When the laser generates heat, the evaporation end heats up, causing the working liquid to evaporate rapidly. The vapor flows to the condensation end due to the pressure difference, releasing heat through the fan, and condensing back into liquid. The liquid returns to the evaporation end via the wick (in gravity heat pipes, the liquid adheres to the pipe wall and flows back due to gravity). This continuous cycle transfers heat from inside the laser to the outside.
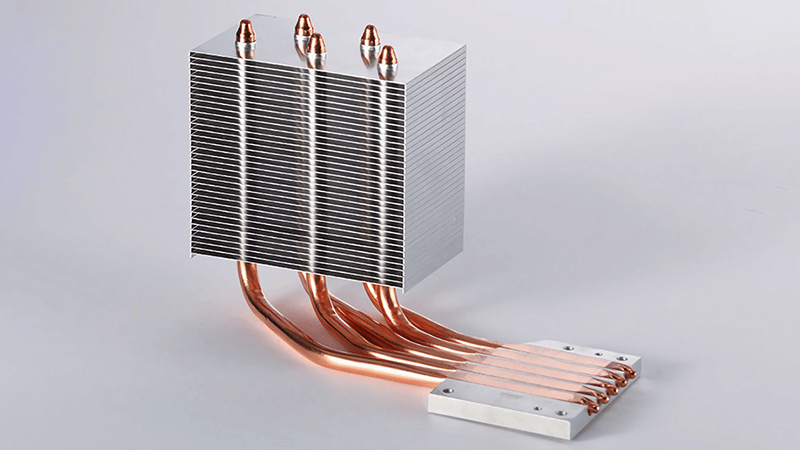
3>. Compressor Cooling
The principle of compressor cooling involves compressing the refrigerant into a high-temperature, high-pressure gas, which then flows to the external condenser. The gas condenses into a low-temperature, high-pressure liquid, and the heat generated is expelled outside by a fan. The low-temperature, high-pressure liquid refrigerant is depressurized by the expansion valve, becoming a low-temperature, low-pressure vapor that flows to the internal evaporator. The evaporator absorbs heat, lowering the laser's internal temperature, and the refrigerant vaporizes into a high-temperature, low-pressure gas. This gas is then compressed again, repeating the cycle for continuous cooling.
3. Comparison of Cooling Methods
Fan cooling has a relatively simple structure, merely dispersing heat from the heat sink to the heat sink fins and using the temperature difference between the fins and the surrounding air to dissipate heat through forced convection by the fan. In summer, when the ambient temperature is high, the temperature difference between the fins and the air is small, significantly reducing cooling capacity. It can only provide passive cooling, greatly influenced by the environment, and cannot accurately control temperature. Its advantage is the simplicity of the overall equipment and control system.
Heat pipe cooling adds the complexity of the heat pipe to the fan cooling system. It uses the evaporation and condensation of the working fluid to rapidly transfer heat from the heat sink to the fins, then dissipating the heat into the air using a fan. It also provides passive cooling, cannot accurately control temperature, and is significantly affected by the surrounding temperature.
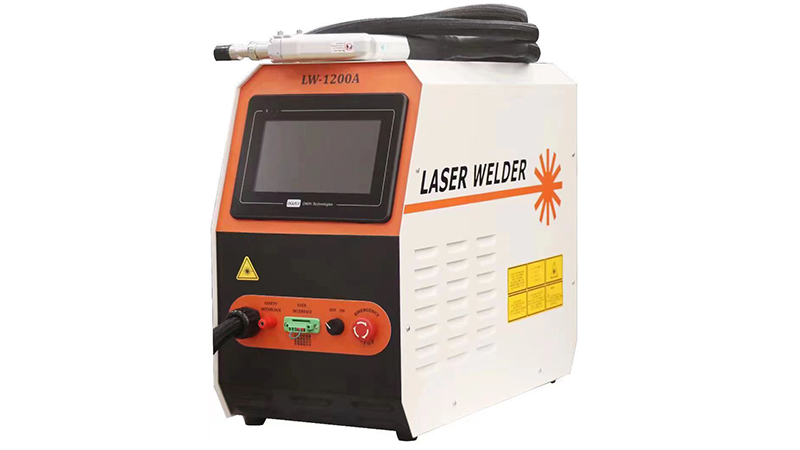
Compressor cooling is an active cooling method. Due to the presence of a compressor and expansion valve, the flow and pressure of the refrigerant can be adjusted to accurately control temperature. The refrigerant temperature in the condenser is higher than the heat sink, facilitating rapid heat transfer to the air. Its control system is more complex; additionally, its structure is more complex than the previous two methods, increasing the size and weight of the equipment accordingly.
Traditional fiber lasers mostly use water cooling, where a compressor first cools the water, which then cools the laser. GW Laser’s air cooling solution directly uses compressor cooling for the laser, eliminating the need for water and intermediary heat transfer stages, thereby enhancing cooling efficiency and reducing size and weight.
What Are Air-Cooling Fiber Laser Welding Machines?
Air-cooling fiber laser welding machines use fans to dissipate heat generated during operation. These machines are generally more compact and easier to maintain.
Pros:
- Simplicity: Fewer parts mean less that can go wrong.
- Cost-Effective: Lower initial investment and maintenance costs.
Cons:
- Limited Cooling Efficiency: Less effective at managing heat, which can impact performance in high-demand situations.
- Noise: If you choose the welding mode with fans. Then it can be noisy, which might be an issue in a quieter working environment.
What Are Water-Cooling Fiber Laser Welding Machines?
Water-cooling fiber laser welding machines, on the other hand, use a liquid coolant to manage heat. This method is more efficient but comes with its own set of challenges.
Pros:
- Superior Cooling Efficiency: Better for prolonged and intensive use.
- Quieter Operation: Less noise compared to air-cooling systems.
Cons:
- Complexity: More parts mean more potential points of failure.
- Higher Costs: Relatively high maintenance costs because of more components.
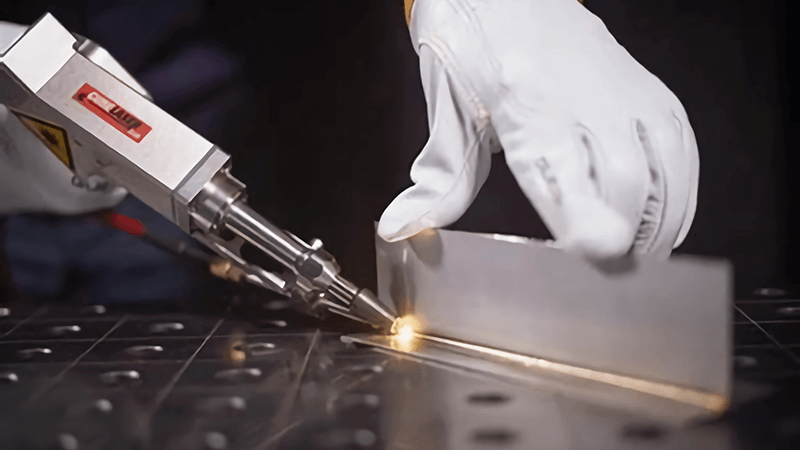
Which One Should You Choose?
1>. Factors to Consider
When deciding between air-cooling and water-cooling, consider the following factors:
- Budget: Water-cooling systems are generally more affordable, while air-cooling can be slightly more expensive.
- Usage Intensity: Water-cooling is better for high-intensity, prolonged use.
- Environmental Requirements: Water-cooling has lower environmental requirements and can generally operate between -20°C to 60°C. However, air-cooling cannot work continuously in high-temperature environments.
- Maintenance Capability: Do you have the resources to maintain a more complex system?
2>. Use Cases
- Small Manufacturing Business: Both water-cooling and air-cooling are sufficient and more economical choices.
- Large Industrial Applications: Water-cooling can offer the reliability and efficiency needed for large-scale operations.
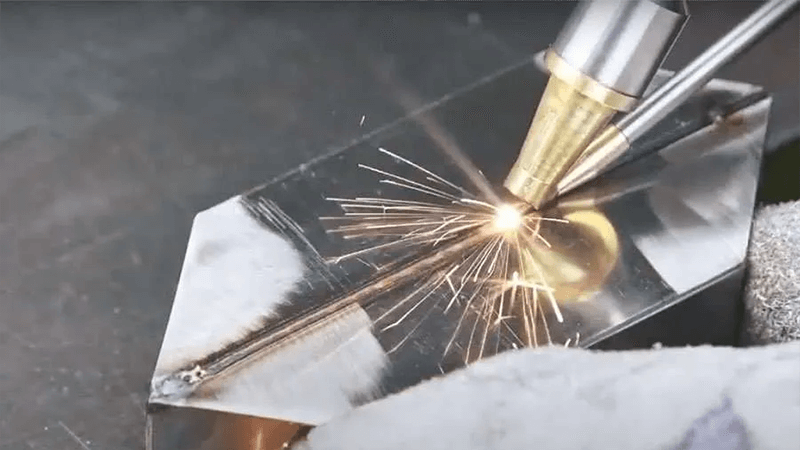
Conclusion
Choosing between air-cooling and water-cooling fiber laser welding machines depends on your specific needs and circumstances. Air-cooling systems are cost-effective and easier to maintain, while water-cooling systems offer superior performance and efficiency for more demanding applications.
So, what's your choice? Will you go for the simplicity of air-cooling or the powerhouse efficiency of water-cooling? Either way, you're making a smart investment in the future of your production capabilities.
For more detailed insights and data, check out to contact us.