Introduction
Ever wondered how to weld aluminum with laser precision? You're in the right place. As a sales engineer at Kirin Laser, I’ve seen firsthand how laser welding can transform aluminum projects. It’s a game-changer, trust me.
Aluminum's high thermal conductivity and low melting point mean that it requires a different approach than other metals. It's all about having the right knowledge and tools to turn these challenges into seamless, strong welds. Laser welding is becoming the go-to method for joining aluminum, thanks to its precision and efficiency. Whether you’re in the aerospace, automotive, or manufacturing industry, understanding laser welding can give your projects a significant edge.
Curious to know how to tame this beast? Read on.
What Makes Laser Welding Ideal for Aluminum?
Laser welding is like magic when it comes to aluminum. The focused laser beam provides precision and control, making it ideal for this highly conductive material.
Aluminum's reflectivity can be a challenge, but with the right settings and equipment, laser welding can create clean, strong welds with minimal distortion.
What Tools and Equipment Do You Need?
To weld aluminum effectively, you need the right tools. A high-quality laser welding machine is essential. These machines offer precision and control that are unmatched by traditional welding methods.
Safety gear is also non-negotiable. Welding helmets, gloves, and protective clothing are your best friends here. Remember, safety first!
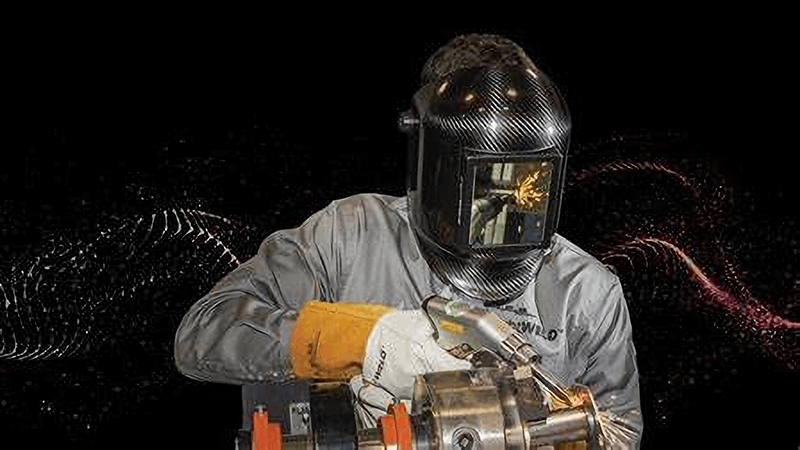
How Should You Prepare for Laser Welding?
Preparation is key when welding aluminum. Start by cleaning the aluminum surface thoroughly. Any contamination can lead to poor weld quality. Use a dedicated stainless steel brush to remove oxides from the aluminum surface.
Next, set up your welding machine. For laser welding, ensure your machine is calibrated correctly and set to the appropriate power and speed settings for aluminum.
What Are Common Challenges and How to Overcome Them?
Welding aluminum isn’t without its challenges. Issues like porosity, cracking, and reflectivity can complicate the process. Porosity occurs due to trapped gases, leading to weak welds. To mitigate this, ensure proper cleaning and use of shielding gases.
Cracking is another issue, often due to the high thermal conductivity of aluminum. To prevent this, control the heat input carefully and use pre-heating if necessary.
What Should You Do After Laser Welding?
Once you've completed the weld, it's time for inspection. Check for any signs of defects, such as cracks or porosity. If you spot any issues, address them immediately to ensure the integrity of your weld.
Finishing touches are also important. Clean the welded area to remove any residual flux or contaminants. This not only improves the appearance but also ensures the durability of the weld.
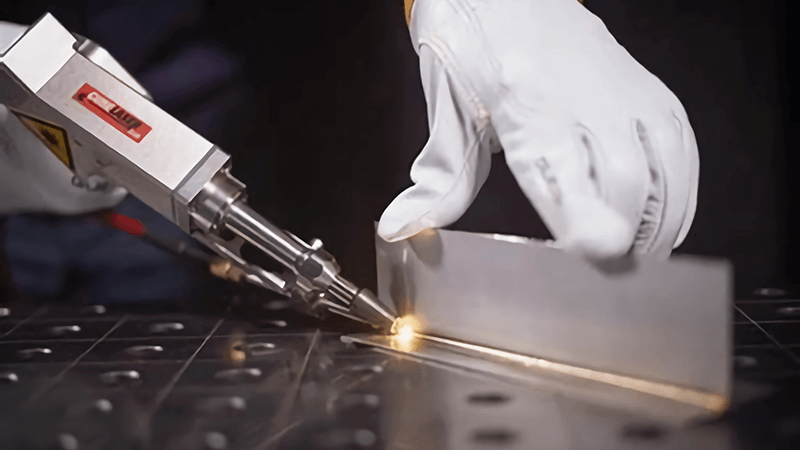
Frequently Asked Questions About Laser Welding Aluminum
What is the Best Laser Welding Method for Aluminum?
Both keyhole and conduction welding can be effective, depending on the material thickness. Keyhole welding is better for thicker materials, while conduction welding is suitable for thinner materials.
How Do You Prevent Reflectivity Issues?
Using a laser with a suitable wavelength and ensuring proper surface preparation can help reduce reflectivity issues.
Why Does Aluminum Weld Look Different?
Aluminum welds can appear different due to their reflective surface and the oxide layer that forms during welding. Proper cleaning and technique can improve the appearance.
What Safety Precautions Should I Take?
Always wear appropriate safety gear, including welding helmets, gloves, and protective clothing. Ensure your workspace is well-ventilated and free from flammable materials.
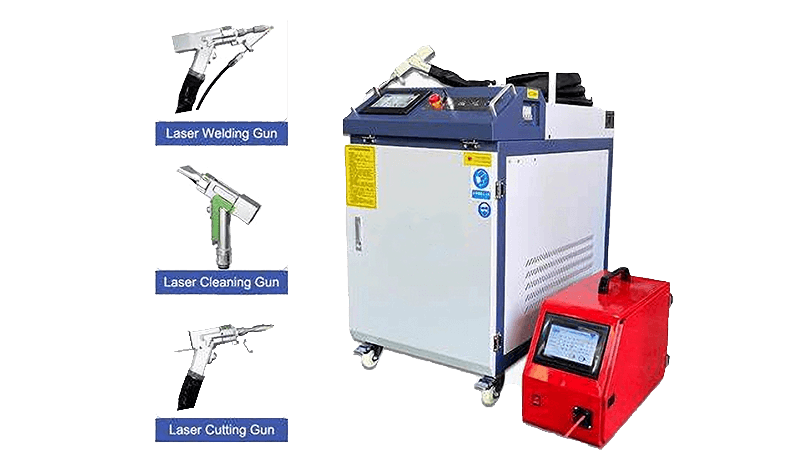
Can You Weld Aluminum with Any Laser?
Not all lasers are suitable for aluminum. Ensure you use a laser with the right power and wavelength for the best results.
How Important is Cleaning Before Welding?
Cleaning is crucial. Any contamination can lead to defects in the weld. Use a dedicated brush and clean the surface thoroughly before welding.
Is it easy to operate laser welding machine for aluminum weld?
The laser welding machines feature a simple, intuitive interface. After just two training sessions, even beginners can use them confidently. The system supports multiple languages for ease of use in your preferred language. The welding process is straightforward and easy to learn, unlike traditional welding methods that require professional skills.
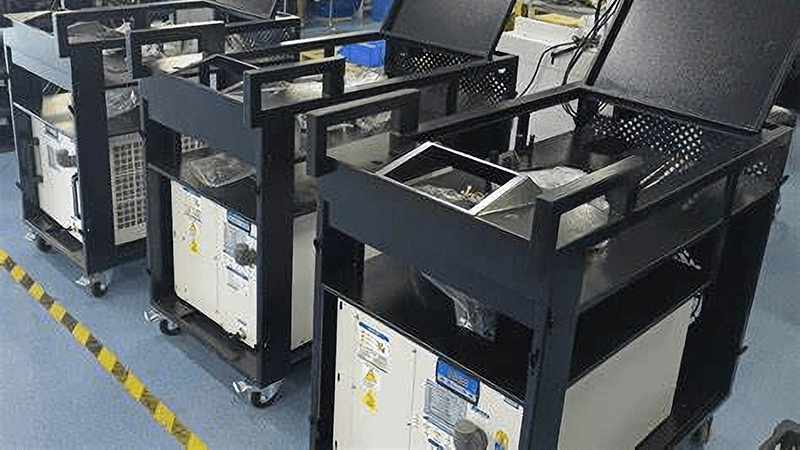
Laser Welding Parameters for Aluminum
Material | Thickness | Scanning Speed | Scanning Width | Power | Wire Model | Wire Speed |
Aluminum | 1 | 300 | 3 | 500 | ER5356 1.0 | 60 |
2 | 300 | 3 | 800 | ER5356 1.2 | 60 | |
3 | 300 | 3 | 1400 | ER5356 1.2 | 60 | |
4 | 300 | 3 | 1800 | ER5356 1.6 | 60 | |
5 | 220 | 3 | 2000 | ER5356 1.6 | 50 |
Conclusion
Laser welding aluminum might seem daunting, but with the right tools, techniques, and a bit of practice, anyone can master it. Remember, preparation is key, and attention to detail can make all the difference. Happy welding!
Reference
1>. "What causes aluminum TIG welds to go grey?" from weldingwed.
2>. "Laser Welding Aluminum" from EB Industries.